Volkswagen estrenará una nueva generación de propulsores eléctricos basados en la eficiencia y el rendimiento. Fueron presentados bajo la denominación interna APP550 y se harán realidad en el nuevo buque insignia eléctrico del fabricante alemán, el ID.7. En su desarrollo ha participado el Departamento Técnico de Volkswagen Turismos con el objetivo de que se implemente en los futuros modelos con plataforma MEB. Se ensambla en el centro tecnológico del Grupo Volkswagen en el centro de competencia Kassel, que cuenta con 15 años de experiencia en el desarrollo de propulsores eléctricos.
Con cada nueva generación, los fabricantes de vehículos eléctricos afinan sus motores y sus transmisiones con dos objetivos fundamentales: mejorar la autonomía y el rendimiento. La tecnología de los propulsores eléctricos avanza al mismo ritmo que lo hacen otros componentes, logrando que los clientes reciban vehículos mucho más avanzados que los que podrían encontrar hace diez años.
A esta misma filosofía responde el nuevo tren motriz que Volkswagen ha creado para los vehículos eléctricos basados en la plataforma MEB. Los ajustes en el diseño de los propulsores están destinados a obtener más por menos. O, dicho de otro modo, lograr más par motor, más eficiencia y mejor autonomía en el mismo espacio.
El nuevo APP550 de tracción trasera genera 163 kW (281 CV) y 550 Nm de par, aunque esta cifra depende de la transmisión de una sola velocidad que hace de intermediaria con el que llega a las ruedas. Reducir la relación de transmisión multiplica el par. Esa es la razón por la que un automóvil de combustión convencional, con una caja de cambios manual, puede hacer girar las ruedas en la primera velocidad, pero no en la tercera. En un coche térmico hay que reducir para obtener par en las ruedas cuando se afronta una pendiente.
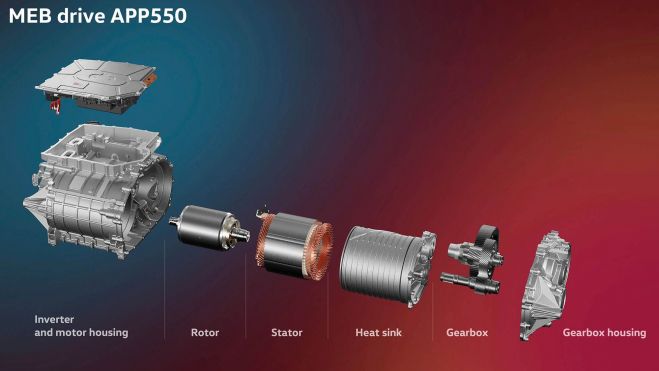
Por eso, Volkswagen advierte que no deben confundirse los 550 Nm de par con la salida en el eje del motor, sino que es el que se envía a las ruedas motrices después de haber pasado por la reductora.
Para elevar el rendimiento general del tren motriz, Volkswagen parte de la misma estrategia que se ha empleado durante más de 100 años con los motores de combustión. Ha encontrado formas de extraer más potencia mecánica de la misma cantidad de energía. La diferencia es que la energía está en forma eléctrica y no en el calor procedente de la quema de combustible.
Volkswagen emplea motores síncronos con un rotor equipado con imanes permanentes más potentes y resistentes y con la mínima cantidad de tierras raras necesarias. Los imanes en el rotor responden al magnetismo del estator sincronizando sus velocidades, de ahí el término ‘motor síncrono’. El uso de chapas eléctricas especiales y nuevos procesos de mecanizado colabora en la consecución de un sistema más eficiente.
Los devanados del estator han aumentado su número y los cables utilizados tienen una sección transversal más grande, por lo que ahora son más gruesos. Al mismo tiempo, el sistema de transmisión se ha reforzado para soportar un par mucho más alto.
El inversor es el cerebro que convierte la electricidad de corriente continua (procedente de la batería) y corriente alterna (la que recibe el motor). En el nuevo motor se ha rediseñado. Puede manejar corrientes más altas y el software se ha mejorado para que el motor convierta la electricidad en energía mecánica de manera más eficiente.
En lugar de usar una bomba eléctrica para el sistema de gestión térmica, que requiere mucha energía, el sistema se enfría automáticamente al permitir que los engranajes y otros componentes de la transmisión distribuyan el aceite. Una vez que este se calienta, se recolecta y se enfría.
Por lo tanto, al examinar al detalle cada parte del motor y de la transmisión del automóvil y realizar mejoras, los ingenieros han mantenido el mismo plan de trabajo que se ha seguido con los motores de toda la vida, cambiando sencillamente la fuente de energía.