Ayer mismo nos hacíamos eco de la pequeña actualización que ha hecho Tesla en el Model Y para el mercado chino: cambios sutiles, pero bien recibidos. Sin embargo, el Model Y podría estar ya beneficiándose de uno de los mayores y más importantes cambios que podrá recibir y que permitirá a Tesla hacer los coches de manera más rápida y más barata.
Según ha filtrado la prensa china después de una reciente visita a la fábrica de Tesla en Shanghái, la compañía estadounidense ha empezado a adoptar la versión 2.0 de su tecnología de fundición a presión, conocida como "Gigacasting", con la que pretende cambiar la manera en que se fabrican los coches en serie.
La tecnología de fundición a presión permite crear, gracias a enormes prensas, los complejos subchasis del coche en una sola pieza, en lugar de las varias decenas de piezas que necesitan ser unidas mediante soldadura o pegamento en un proceso convencional. Es un cambio que el cliente no percibe a simple vista, pero es una modificación muy importante para el fabricante.
Cuando Tesla lanzó el Model Y al mercado, simplificó enormemente el proceso de producción en comparación con el Model 3. El subchasis trasero del Model Y está hecho de dos grandes piezas de metal, en lugar de las setenta que eran necesarias en el Model 3 (el nuevo Model 3 ya utiliza también esta tecnología). Esto permite reducir el número de robots en la fábrica, facilita hacer coches de manera más rápida y reduce los costes de fabricación.
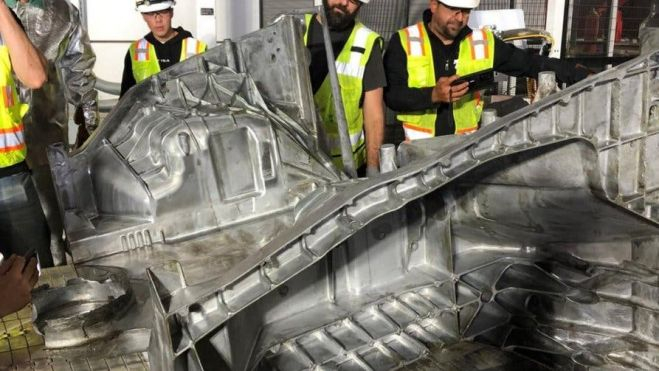
Ahora, el siguiente paso es hacer los subchasis de una sola pieza de metal, lo que incrementaría significativamente la productividad. Además, esta técnica permite reducir en hasta un 40% los costes de montaje del subchasis trasero en comparación con los métodos tradicionales. También rebaja el peso de la pieza en un 10%, lo que redunda en menos consumo del vehículo y mayor autonomía.
Esta tecnología de fundición a presión está provocando cambios en la industria automotriz y son ya varios los fabricantes que han adoptado, o planean adoptar, este proceso. Geely ha empezado a utilizar la fundición a presión de una sola pieza en el Zeekr 009, su espectacular monovolumen eléctrica, eliminando la necesidad de hacer casi 800 soldaduras y reduciendo el número de piezas en más de 80. Volvo, que pertenece al mismo grupo, también empezará a utilizar esta técnica. Xpeng, asimismo, ha implementado esta tecnología en su arquitectura SEPA, con subchasis delanteros y traseros de fundición a presión de aluminio de una sola pieza. Incluso la mismísima Toyota empezará a utilizar esta técnica en su nueva plataforma modular diseñada específicamente para coches eléctricos.